Taking Stock of SiC, Part 2: a review of current SiC power devices
- Peter Gammon
- Mar 10, 2022
- 7 min read
Si power devices are as mature as they will ever get, having reached their material limit. SiC power devices are fast maturing, offering fast switching, efficient device performance in the automotive sector. Yet, they remain a long way from reaching their full potential. So just how good are these devices today? In this blog, we tackle that question and explain how SiC will be essential in the drive to 800V+ EV systems.
Over the last year at PGC Consultancy, we have gathered together a large amount of data on today’s SiC MOSFETs. We have analysed countless datasheets, and independently tested and scanned SiC devices to benchmark their performance. This data can be used to give a good snapshot of the technology today, and to predict its improvement in the future.
In this post we shall present a current snapshot of SiC technology, benchmarking today’s SiC MOSFETs against Si MOSFETs, Si IGBTs, and SiC’s theoretical performance limit. This data helps to frame the crucial role that 1200V SiC technology is likely to have in the transition from notional 400V system ratings to 800V and beyond.
This post follows on from Taking Stock of SiC, Part 1, in which the costs of a SiC device are analysed, breaking down the reasons for a SiC MOSFET costing 2-3x the cost of an equivalent Si IGBT, and attempted to predict how the price of these might reduce over time.
Mapping today’s SiC power devices
Plotted on a unipolar limit graph in the Figure are today’s state of the art SiC MOSFETs from a number of device manufacturers, from the 650, 1200 and 1700 voltage classes, and a large range of current/resistance classes. Their specific on-resistance (rated resistance × die size) is plotted against their rated voltage. The same data for a range of Si MOSFETs are presented for reference, as well as two IGBTs, using their differential on-resistance (thus ignoring their turn on voltage).
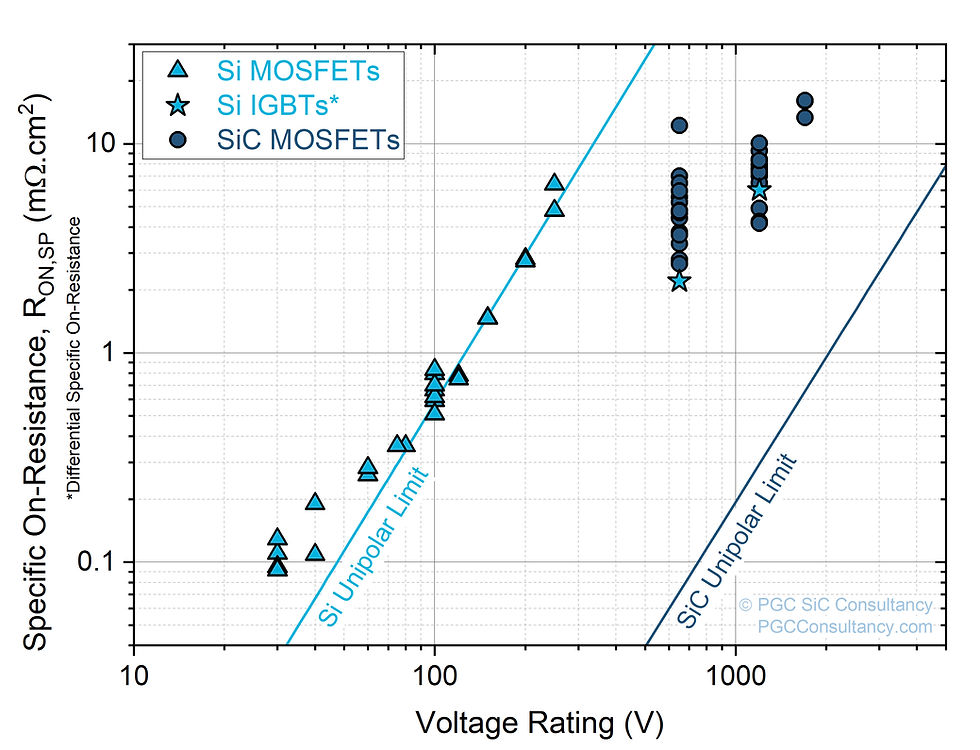
Also plotted, in long diagonal lines, are the limits of each material, the lowest resistance possible in Si, or SiC, for a given voltage rating. Known as the unipolar limit of the material, these exist because a wide, low doped drift region is necessary to block a large voltage in the off-state, and yet its low doping adds considerable resistance to the device in the on-state. This unavoidable trade off means that each 2x increase in the breakdown voltage of a MOSFET will drive up the resistance of the device by about 4.5x.
A crucial point to remember with these graphs is that if a device sits away from the ideal unipolar limit, it may still be an excellent device. However, it will occupy more wafer space than a device that is on, or near, the limit, so it will likely cost more. From the manufacturer’s perspective, if the device they produce sits on the Unipolar limit, at the very limit edge of the technology, then they have maximised the number of devices of that voltage/current rating that they can fit on a wafer, maximising yield.
So, while this plot tells us little
about how fast we operate the devices, or their thermal performance, or their reliability, etc, what it does tell us is how close a company’s technology is to being optimal from a production and yield point of view.
As we saw in Part 1 of the Taking Stock series, such resistance reductions will play a significant part in the overall cost reduction of SiC power devices in the future.
Silicon Power Devices: An Essential Frame of Reference
Devices made from silicon are the natural benchmark for SiC, and the ideal place to start. With the material quality of Si having been perfected over decades, through numerous generations of device design improvement, it has almost nothing that prevents it reaching the ideal technology curve. The latest Si MOSFET devices, analysed for this work, are so good that they appear on, or even beneath, the Unipolar Limit, which perhaps highlights the margins of error of my Unipolar Limit calculation! Only below 100 V are the limits of Si MOSFETs becoming apparent, as the total device resistance becomes dominated by fixed resistances, the substrate, JFET and channel resistances, rather than the scalable drift region resistance.
Also plotted are two examples of Si IGBTs, a device that is ubiquitous within medium voltage power electronic applications. The bipolar class of devices use minority carriers (holes) as well as the majority carriers (electrons) to flood the low resistance drift region with carriers when it is on, so lowering the region’s resistance. Hence, these devices appear below silicon’s unipolar limit. However, this conductivity modulation (as it is known) comes at a price: the act of injecting and removing all the minority carriers takes time and results in significant switching losses.
Prior to the emergence of SiC, the Si picture summarises well the binary choice of a circuit designer. Opt for fast switching MOSFETs at low voltage, or slow switching IGBTs at medium-high voltages (and a slightly more interesting middle ground with superjunction MOSFETs in between – a topic for another day).
(Note: Another feature of an IGBT is its turn-on voltage, which is present due to a p-n junction beneath the drift region. This turn-on voltage can’t well be captured on a unipolar graph, but it means that the actual forward voltage drop of an IGBT is higher than implied in the Figure by plotting the differential resistance alone.)
So how good is SiC today?
Returning to the theme, and against the backdrop of the field of Si devices, the range of SiC MOSFETs plotted tell us much about the technology today. Here we run through a number of key takeaways from the range of SiC devices plotted:
The SiC devices with the lowest resistivity come from one manufacturer, whose products consistently have the lowest specific resistance.
1. A wide spread of results. Looking at the SiC devices plotted, there is significant dispersion within each voltage class. However, what unites the devices with the lowest resistivity plotted is first, that they have the highest current ratings. They are therefore large chips with large active areas, and hence a smaller proportion of the chip is given over to non-current carrying regions, such as the gate pad, and termination regions.
Second, the devices with the lowest resistivity come from one manufacturer, whose products consistently have the lowest specific resistance and smallest chip sizes. Indeed, there is significant spread across manufacturers, in part favouring those who have most recently launched new products. However, there is a clear trend suggesting some manufacturers are over designing their products, effectively derating their devices by designing them to support much greater voltages than their rating. This derating is another theme for Part 3 of this Taking Stock series.
2. At 650V, SiC is good… Unlike the Si devices plotted, today’s young SiC MOSFETs sit a long way from their unipolar limit. This is particularly true at 650V; indeed the resistance is high enough that today’s 650V trench gated field-stop IGBT variants have slightly lower conduction losses than the SiC MOSFET. Despite this, the very fact that SiC resistivity is even in the same ballpark as a bipolar, conductivity modulated, Si IGBT, means that as we switch both devices at any practical frequency, the relatively small increase in conduction losses is eclipsed by the IGBTs large switching losses. This is what enables the faster switching, higher efficiency solution, demonstrated at 650V by Tesla, whose 2018 Model 3 inverter was reported to be almost 40% of the weight of a Nissan Leaf’s despite delivering more than 2x the power. The efficiency gains will have permitted a reduction in the number of expensive and heavy batteries required in the vehicle, so repaying the relatively small component costs.
3. …but at 1200V, SiC is excellent. As much as SiC has proven itself at the 650V range, 1200V devices are much closer to the material’s “sweet spot”. At 1200V, SiC MOSFETs have a unit area resistance closer to the SiC unipolar limit, sitting 14-33x above it, compared to 35-90x at 650V. The reason for this is that at 650V, the resistance is dominated by fixed resistances, from the channel and substrate, rather than solely the drift region, from which the unipolar limit is calculated.
The benefit of this is borne out when 650 and 1200V SiC MOSFETs are benchmarked against Si IGBTs of the same voltage and current rating. In the table below, the already impressive performance of a 650 V SiC MOSFET replacing a 650V Si IGBT includes twice the power density and 6.5x lower switching losses. These values jump up at the higher voltage however, a 1200 V SiC device replacing a 1200V Si IGBT having 16x greater power density and 11x lower switching losses. The relative size difference of the two devices is also shown.

This switching benefit at 1200V is explored in a recent paper [1], wherein 1200V MOSFET modules were compared against equivalent Si IGBT modules in a 135kVa test setup. Switching at low frequency (<4kHz) whereby conduction losses dominate, the total losses from the two setups were equal, at approximately 1%. At higher frequency, however, the switching losses in the IGBT setup increase steeply, forcing the total losse up to 1.8% at 12kHz, and 2.5% by 20kHz. By contrast, the total losses of the SiC MOSFET module, relatively unburdened by switching losses at these frequencies, reaches only 1.4% at 20kHz.
SiC is a key enabler for 800V electric vehicles
The trend in the EV market to double the 400V system standard to 800V has a number of benefits. These benefits derive from the simple notion from the equation Power = Voltage × Current, that when delivering a fixed power, doubling the voltage allows current throughput to be halved. This leads to faster charging, due to reduced heating of the battery; smaller, lighter motors due to the reduction of copper windings; and lighter cables wherever this current has to be transported. This has a big impact on overall system efficiency, lengthening range or reducing battery weight, and reducing system cost.
It is clear from the analysis presented of today’s SiC devices, that this semiconductor has a key role to play in maximising the potential of 800V designs. At 1200V, SiC begins to show off, leaving little but reliability concerns, design legacy, and/or conservative application spaces as reasons for sticking with Si IGBTs. This is an open question therefore for the recent Porsche Taycan in which a Si IGBT solution won out despite the transition to 800 V, while simultaneously, the 900V Lucid Air opted for SiC MOSFETs.
In summary, Si technology is about as mature as it will get, with MOSFETs on the technology limit, and highly mature IGBT technology. SiC is a youngster by comparison, but after only a decade and around 3 generations of devices, SiC MOSFETs stack up well against Si IGBTs. The data evidences something we at PGC Consultancy have long been preaching, that while SiC is undoubtedly good at 650V, it keeps getting better at 1200V and beyond.
In the next Taking Stock post, I will address the question of just how much better SiC can get. This will address the fact that the SiC devices remain some distance from their unipolar limit, breaking down the resistances that cause this, and investigating what margins there are for future improvement.
[1] A. Allca-Pekarovic et al, "Comparison of IGBT and SiC Inverter Loss for 400V and 800V DC Bus Electric Vehicle Drivetrains," 2020 IEEE Energy Conversion Congress and Exposition (ECCE), 2020
SYNCHRO-SYM is a new electric motor circuit and control technology that reduces the 2-3x cost impact of SiC MOSFET devices while improving their performance by 2-3x. www.bestelectricmachine.com